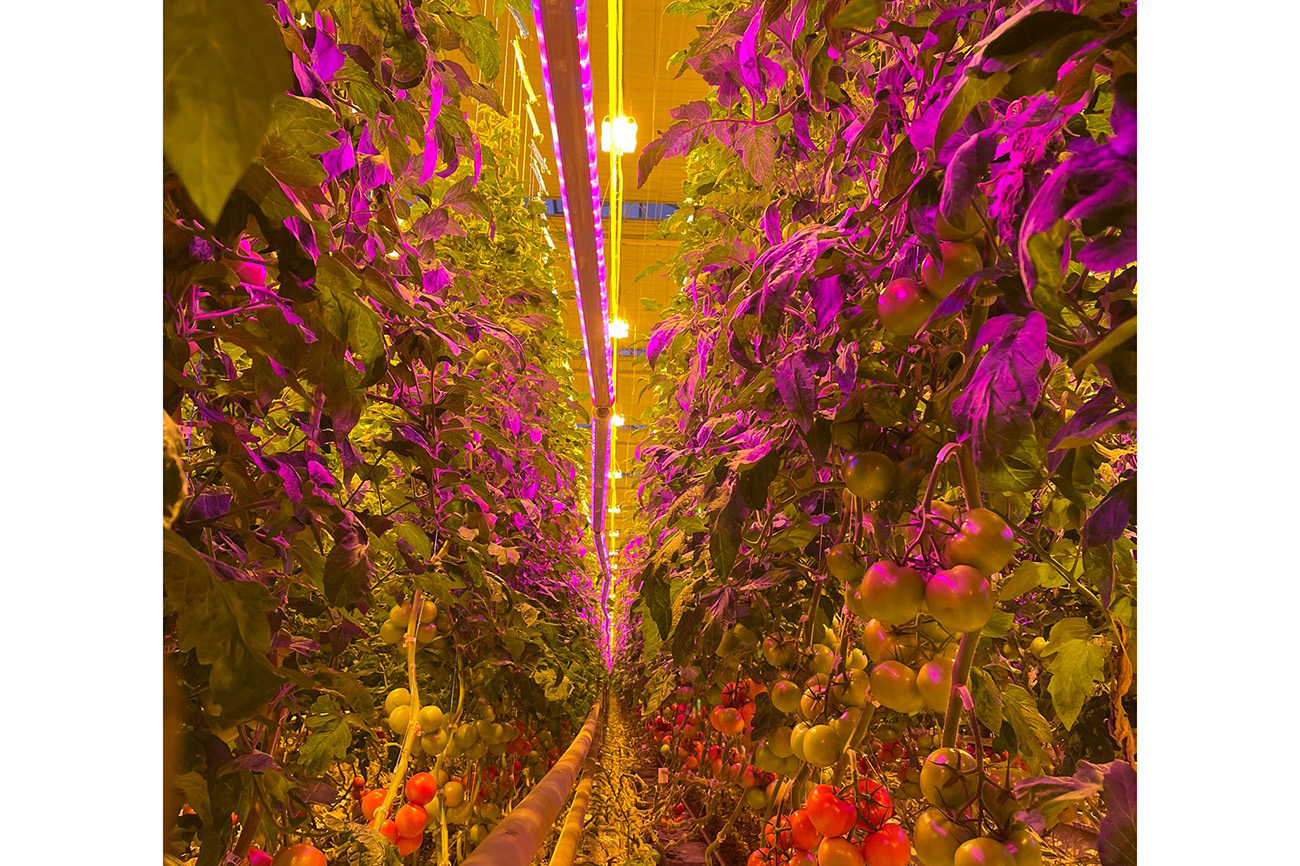
A U.S. greenhouse grower in the Midwest was able to increase its yields of ‘Macxize’ tomatoes-on-the-vine crops by 17 percent by combining intracanopy LED lighting with high pressure sodium top lighting. Photos courtesy of Hort Americas
By David Kuack
Continue reading Can intracanopy/intercanopy LED grow lights be used to increase greenhouse vegetable crop yields?